液化石油气气动切断阀标准规范
日期: 25-03-17 阅读次数:
一、引言
液化石油气(LPG)作为一种广泛使用的燃料,在储存、运输和使用过程中存在一定的危险性。气动切断阀在液化石油气系统中起着至关重要的安全保障作用,确保在紧急情况(如泄漏、超压等)下能够迅速切断气流,防止事故的进一步扩大。为了保障液化石油气系统的安全可靠运行,制定统一、科学的气动切断阀标准规范是非常必要的。
二、液化石油气的特性及其对气动切断阀的要求
(一)液化石油气的特性
易燃性
液化石油气主要成分包括丙烷、丁烷等,这些成分的闪点较低,一旦泄漏遇到火源极易燃烧,这就要求气动切断阀具有高度的密封性,防止任何可能的泄漏。
挥发性
液化石油气在常温常压下容易挥发,形成可燃混合气。气动切断阀需要适应这种挥发性物质的流动特性,确保在不同工况下都能正常工作。
膨胀性
当温度升高时,液化石油气的体积会显著膨胀。气动切断阀应能承受这种体积变化带来的压力变化,并且在设计压力范围内保持可靠的切断功能。
(二)基于液化石油气特性的气动切断阀要求
密封性能
必须具备卓越的密封性能,以防止液化石油气的泄漏。密封材料要能够抵抗液化石油气的腐蚀,并且在长期使用过程中保持密封效果。一般来说,采用特殊的橡胶或金属密封材料,并按照严格的密封试验标准进行检测,如气泡法密封试验,在规定的试验压力下,持续一定时间观察是否有气泡产生来判定密封性能。
快速响应性
在紧急情况下,如检测到泄漏或超压信号时,气动切断阀应能在极短的时间内实现完全切断。响应时间通常要求在数秒之内,这取决于整个液化石油气系统的安全等级要求。为了实现快速响应,气动切断阀的驱动机构要具有足够的动力,并且阀门的运动部件要设计合理,减少运动阻力。
耐压性能
考虑到液化石油气的膨胀性和可能的超压情况,气动切断阀需要具备较高的耐压能力。其设计压力应根据液化石油气系统的最大工作压力确定,并且要有一定的安全余量。在制造过程中,要通过严格的耐压试验,如按照相关标准进行水压试验,试验压力通常为设计压力的1.5倍,持续一定时间,检查阀门是否有变形、泄漏等情况。
三、液化石油气气动切断阀的设计标准
(一)阀门结构设计
阀体
阀体的结构应能够承受液化石油气的压力和腐蚀作用。一般采用铸钢或不锈钢等材质,以确保足够的强度和耐腐蚀性。阀体的内部流道要设计合理,减少流体阻力,避免产生漩涡和紊流,从而提高阀门的流量特性。
阀芯
阀芯是控制阀门开闭的关键部件。其形状和尺寸要与阀体的流道相匹配,确保在关闭状态下能够完全截断气流。阀芯的材质要具有良好的耐磨性和耐腐蚀性,常见的有不锈钢、合金钢等。阀芯的运动方式(如直线运动或旋转运动)也会影响阀门的性能,需要根据具体的应用场景进行选择。
阀座
阀座与阀芯配合实现密封功能。阀座的密封面要进行精密加工,表面粗糙度要达到一定的标准,以保证密封效果。阀座的材质要与阀芯相适应,并且能够承受多次开闭操作的磨损。
(二)驱动机构设计
气动执行器
气动执行器是为阀门提供动力的部件。其工作压力要与液化石油气系统的气源压力相匹配,一般在0.4 - 0.8MPa之间。气动执行器的输出力要足以克服阀门的摩擦力和介质压力,确保阀门能够顺利开闭。执行器的响应速度要快,并且具有良好的调节性能,可以根据控制系统的要求精确调整阀门的开度。
控制信号
气动切断阀的控制信号通常为气动信号或电 - 气转换信号。对于气动信号,其压力范围和信号传输的准确性要符合标准要求。在电 - 气转换系统中,要确保电气元件的防爆性能,以适应液化石油气的危险环境。信号传输的延迟时间要尽可能短,以保证阀门能够及时响应控制指令。
四、液化石油气气动切断阀的制造标准
(一)材料选择与质量控制
原材料采购
制造气动切断阀的原材料必须从合格的供应商处采购。对于钢材等主要材料,要进行严格的质量检验,包括化学成分分析、力学性能测试等。例如,对不锈钢材料,要检查其铬、镍等主要元素的含量是否符合标准,同时进行拉伸试验、硬度试验等力学性能测试。
加工工艺
在制造过程中,要遵循严格的加工工艺规范。阀体的铸造或锻造工艺要保证阀体的内部质量,避免出现气孔、夹渣等缺陷。阀芯和阀座的加工要采用精密的加工设备,如数控机床,以确保尺寸精度和表面质量。对于焊接部位,要进行无损检测,如采用射线探伤或超声波探伤方法,检查焊接质量是否合格。
装配工艺
装配过程是确保气动切断阀性能的关键环节。装配人员要严格按照装配图进行操作,确保各个部件的安装位置准确无误。在装配过程中,要对密封件进行正确安装,避免密封件损坏。装配完成后,要进行整体的调试,检查阀门的开闭功能、密封性能等是否符合要求。
(二)性能测试标准
出厂前测试
每台气动切断阀在出厂前都要进行全面的性能测试。首先进行外观检查,检查阀门表面是否有划伤、锈蚀等缺陷。然后进行密封性能测试,按照规定的试验压力和试验方法进行测试,确保阀门无泄漏。接着进行动作性能测试,检查阀门的开闭是否灵活,响应时间是否满足要求。最后进行耐压性能测试,在规定的试验压力下持续一定时间,检查阀门是否有变形、泄漏等情况。
抽检与批量检验
除了出厂前的逐台测试外,还要进行抽检和批量检验。抽检比例要根据相关标准确定,一般为5% - 10%。对于抽检不合格的批次,要进行整批产品的重新检验或采取相应的整改措施。批量检验项目包括产品的一致性检查、性能指标的统计分析等,以确保整批产品的质量稳定性。
五、液化石油气气动切断阀的安装与维护标准
(一)安装标准
安装位置
气动切断阀的安装位置要根据液化石油气系统的工艺流程和安全要求确定。一般应安装在易于操作、便于维护的位置,同时要考虑到在紧急情况下能够快速切断气流,避免受到其他设备或障碍物的影响。例如,在液化石油气储存罐的出口管道上,应靠近储存罐安装,以减少管道内液化石油气的泄漏量。
安装方向
阀门的安装方向要正确,确保流体按照设计方向流动。对于有方向性要求的阀门,如止回阀与气动切断阀的组合安装,要特别注意安装顺序和方向,以保证整个系统的正常运行。
管道连接
在与管道连接时,要采用合适的连接方式,如法兰连接、螺纹连接等。连接部位要保证密封良好,在安装过程中要按照标准的拧紧力矩进行操作,避免连接过松或过紧。管道与阀门之间要进行良好的接地连接,防止静电积聚。
(二)维护标准
定期检查
要制定定期检查计划,对气动切断阀进行检查。检查内容包括阀门的外观状况、密封性能、动作性能等。定期检查的周期根据阀门的使用频率、工作环境等因素确定,一般为每月或每季度检查一次。
部件更换
在检查过程中发现部件磨损或损坏时,要及时更换。例如,密封件经过一定时间的使用后可能会老化,导致密封性能下降,此时要更换新的密封件。对于阀芯、阀座等关键部件,如果磨损严重影响阀门性能,也要进行更换。更换部件时,要使用符合标准的原厂配件或经过认证的替代配件。
故障排除
当气动切断阀出现故障时,要按照故障诊断流程进行排除。首先要检查控制信号是否正常,然后检查气动执行器的工作状态,最后检查阀门的机械结构。在故障排除过程中,要使用专业的检测工具和设备,如压力表、万用表等,确保故障诊断的准确性。
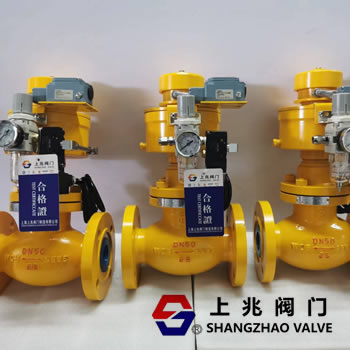